Lean management is a business approach that focuses on maximising value for customers while minimising waste. It originated in the manufacturing sector, specifically within the Toyota Production System, but has since been adopted across various industries worldwide.
For organisations seeking ISO certification in the UK, understanding and implementing lean management principles can significantly enhance operational efficiency, quality, and customer satisfaction. This blog post aims to elucidate what lean management entails and its relevance for those pursuing ISO certification.
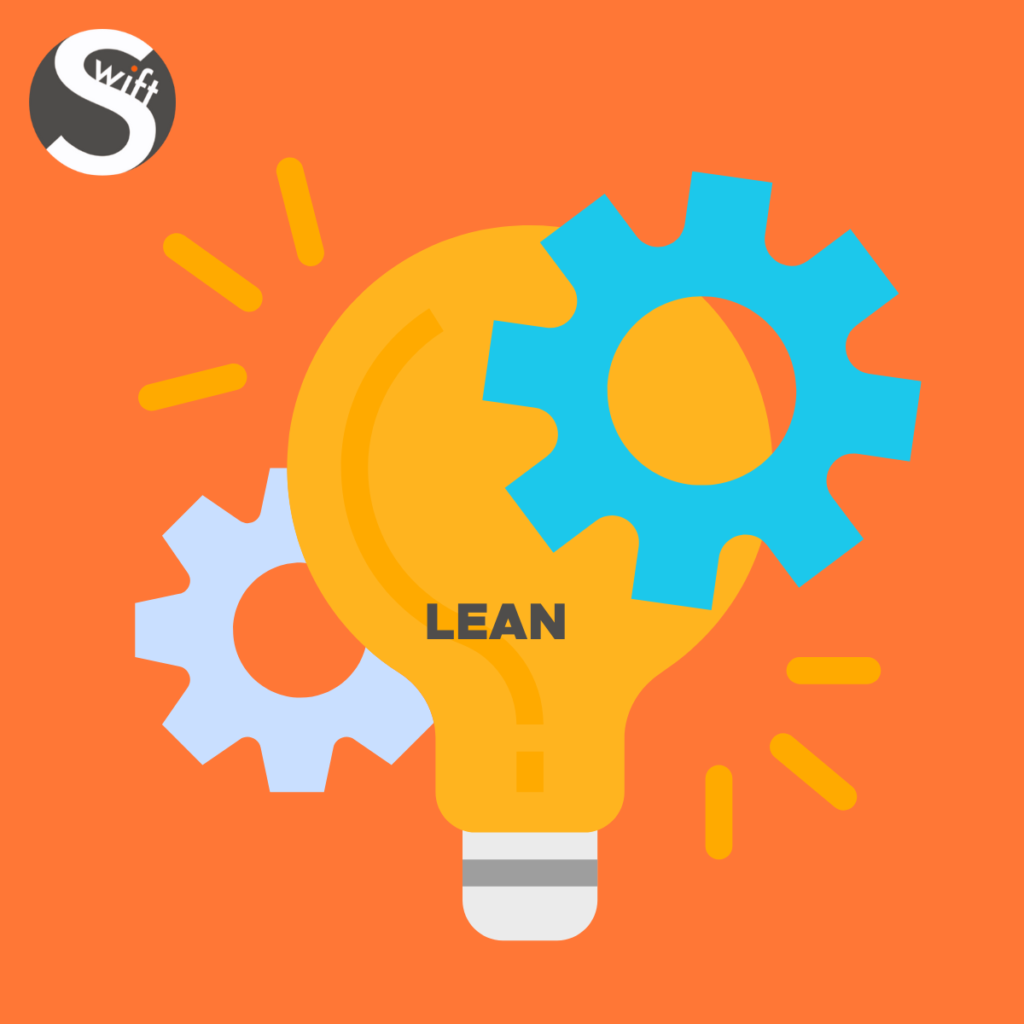
The Core Principles of Lean Management
It has five fundamental principles designed to streamline operations and enhance productivity:
- Value Identification: The first step in lean management is to identify what constitutes value from the customer’s perspective. This principle emphasises understanding customer needs and expectations to ensure that all organisational activities align with delivering that value.
- Value Stream Mapping: Once value is defined, the next step is to map the value stream. This involves analysing the entire process flow, from raw materials to the final product or service, to identify and eliminate non-value-adding activities (waste).
- Flow Creation: Establishing a continuous flow of value-adding activities is essential for this management. This principle focuses on eliminating bottlenecks and ensuring that each step in the process seamlessly transitions to the next, thereby reducing delays and inefficiencies.
- Pull System Implementation: In a lean system, actual customer demand drive production rather than forecasted demand. This principle, known as the pull system, helps reduce overproduction and inventory costs, ensuring that resources are utilised efficiently.
- Perfection Pursuit: It is a continuous improvement journey. Organisations are encouraged to regularly review and refine their processes, striving for perfection by consistently seeking ways to enhance value and eliminate waste.
Types of Waste in Lean Management
It categorises waste into seven types, commonly known as TIMWOOD:
- Transportation: Unnecessary movement of materials or products.
- Inventory: Excess inventory that is not immediately required for production.
- Motion: Unnecessary movement of people or equipment.
- Waiting: Idle time waiting for materials, information, or equipment.
- Overproduction: Producing more than need of the customer.
- Overprocessing: Performing more work or using more resources than necessary.
- Defects: Production errors that require rework or result in scrap.
Understanding these waste types is crucial for organisations to identify inefficiencies within their processes and take corrective actions.
Lean Management and ISO Certification
ISO (International Organisation for Standardisation) certification is a globally recognised standard that demonstrates an organisation’s commitment to quality management and continuous improvement. For UK businesses, obtaining ISO certification can enhance credibility, customer trust, and market competitiveness.
Lean management complements ISO certification by aligning with several key ISO standards, such as:
- ISO 9001 (Quality Management Systems): It’s focus on customer value, process efficiency, and continuous improvement directly supports the requirements of ISO 9001. Implementing lean principles can help organisations meet and exceed the quality management criteria outlined in this standard.
- ISO 14001 (Environmental Management Systems): Lean management’s emphasis on waste reduction and resource efficiency aligns with the environmental sustainability goals of ISO 14001. By minimising waste and optimising resource use, organisations can reduce their environmental footprint and meet the requirements of this standard.
- ISO 45001 (Occupational Health and Safety Management Systems): It promotes a safe and efficient workplace by identifying and eliminating waste, which can include unsafe practices. This aligns with the objectives of ISO 45001, ensuring a safer working environment for employees.
Benefits for ISO Certification
Implementing lean management principles offers several benefits for organisations seeking ISO certification:
- Improved Efficiency: Lean management helps streamline processes, reduce waste, and eliminate inefficiencies, leading to improved operational efficiency. This is a critical factor in meeting the process efficiency requirements of ISO standards.
- Enhanced Quality: By focusing on value and continuous improvement, lean management promotes higher quality products and services. This aligns with the quality management criteria of ISO standards, helping organisations achieve and maintain certification.
- Cost Savings: Lean management’s emphasis on waste reduction and resource optimisation leads to significant cost savings. These savings can be reinvested into quality improvement initiatives, further supporting ISO certification efforts.
- Customer Satisfaction: Lean management prioritises customer value, ensuring that products and services meet or exceed customer expectations. This focus on customer satisfaction is a key component of ISO standards, helping organisations build stronger relationships with their clients.
- Employee Engagement: Lean management encourages employee involvement in continuous improvement efforts, fostering a culture of engagement and collaboration. This is vital for maintaining the high standards required for ISO certification.
Steps to Implement Lean Management
For organisations in the UK aiming for ISO certification, the following steps can facilitate the implementation of lean management principles:
- Conduct Training: Educate employees about lean management principles and the benefits of ISO certification. Training programs can help build a shared understanding and commitment to lean initiatives.
- Perform a Value Stream Analysis: Analyse current processes to identify value-adding and non-value-adding activities. This analysis will serve as the foundation for developing a lean management strategy.
- Set Clear Goals: Define specific, measurable goals for lean management initiatives. These goals should align with the requirements of the relevant ISO standards and support the organisation’s overall objectives.
- Implement Lean Tools: Utilise lean tools such as 5S (Sort, Set in order, Shine, Standardise, Sustain), Kaizen (continuous improvement), and Kanban (visual management) to facilitate process improvements.
- Monitor and Adjust: Regularly review the progress of lean management initiatives and make necessary adjustments. Continuous monitoring and improvement are essential for sustaining lean practices and achieving ISO certification.
How to Get ISO Certification?
ISO Certification costs vary depending on your business, we offer competitive pricing and a unique client led approach to our auditing services. Contact us today for a FREE, no obligation quote – Call us on 0161 470 5352 or fill out a form here and a member of our team will be in touch.
Conclusion
Lean management is a powerful approach that can significantly enhance an organisation’s operational efficiency, quality, and customer satisfaction. For businesses in the UK seeking ISO certification, implementing lean management principles can provide a robust foundation for meeting and exceeding the requirements of various ISO standards. By understanding and embracing lean management, organisations can not only achieve ISO certification but also drive continuous improvement and long-term success.